Frequent Downtime on Your Automotive Assembly Line? 3 Key Solutions to Prevent False Alarms in Safety Light Curtains
- Share
- publisher
- Zoe
- Issue Time
- Mar 21,2025
Summary
Struggling with safety light curtain false alarms on your automobile assembly line? Learn how to troubleshoot common safety light curtain errors, reduce downtime, and optimize performance with expert solutions.
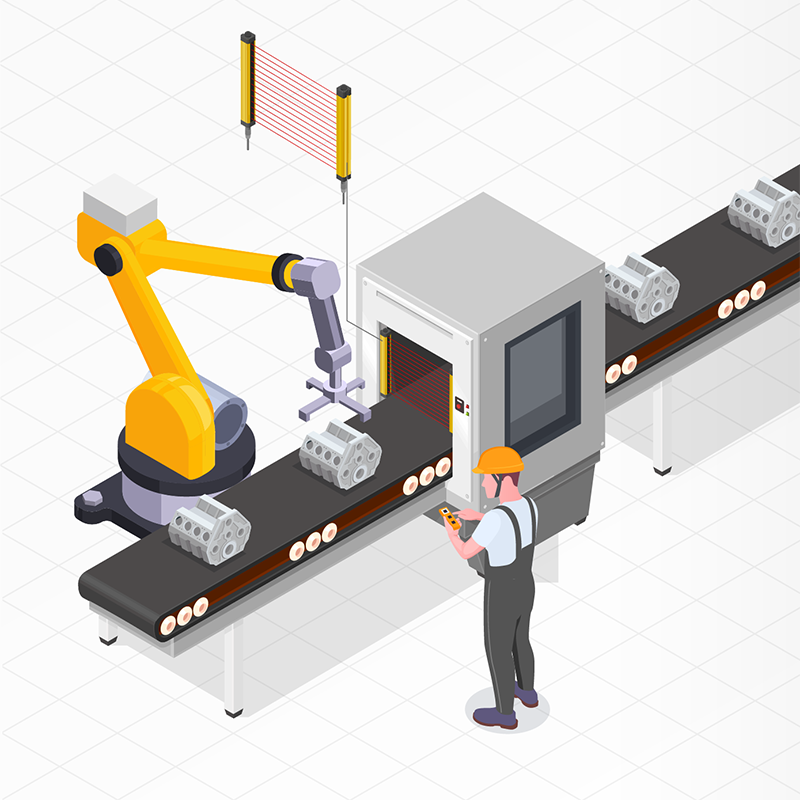
In the highly automated automotive assembly process, every production line must operate seamlessly to ensure efficiency and profitability. However, a major automobile manufacturer recently encountered a critical issue—frequent false alarms in safety light curtains, causing unexpected production halts.
Safety Light Curtain False Alarms Disrupting Production
Safety light curtains are designed to protect workers and equipment, but in this case, they became a source of production downtime instead. With an average of 2-3 false triggers per hour, the assembly line had to stop unexpectedly, leading to:
Significant financial losses, exceeding $5,000 per hour due to idle machines and disrupted workflows.
Delayed order fulfillment, resulting in potential contract penalties.
Inefficient labor usage, as workers had to wait for production to resume.
These challenges highlighted the urgent need for effective troubleshooting of safety light curtain errors to restore efficiency.
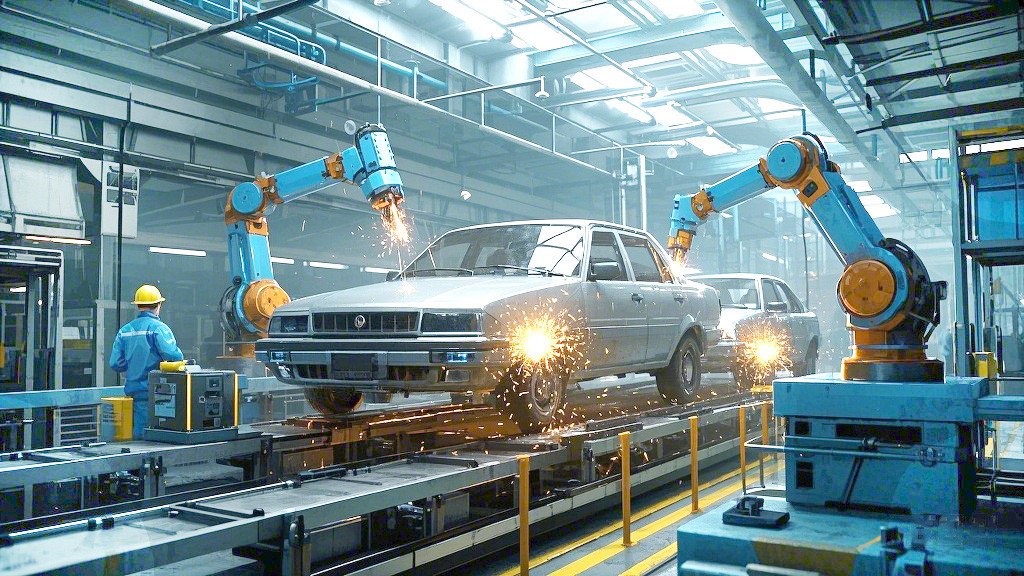
Root Causes of Safety Light Curtain Errors
1. Environmental Interference: Hidden Risks in the Workshop
The complex environment of an automotive assembly line can negatively impact safety light curtain performance. Key factors include:
Welding sparks: These bright flashes can be misinterpreted as an obstruction, causing unnecessary emergency stops.
Metal dust and debris: Accumulated dust can interfere with the infrared beams, leading to inconsistent signal transmission and false alarms.
2. Mechanical Vibration: The Impact of Equipment Movement
High-speed robotic arms and conveyor systems generate vibrations that affect the alignment of safety light curtains:
Sensor misalignment due to continuous machine vibrations can disrupt the infrared beam connection, triggering alarms.
Resonance effects: When the vibration frequency matches the natural frequency of the installation structure, misalignment issues become more frequent.
3. Incorrect Parameter Settings: Response Time Not Optimized
Safety light curtain response time plays a crucial role in preventing errors. In this case:
Fast-moving robotic arms passed through the detection zone too quickly for the light curtain to process accurately.
Delayed signal processing led to false alarms, stopping the assembly line unnecessarily.
Three Engineering Solutions to Solve Safety Light Curtain False Alarms
1. Interference-Resistant Technology Upgrade: Enhancing the Safety Light Curtain’s Environmental Adaptability
🔹 High-Efficiency Filtering Technology for Optimized Anti-Interference Performance
We employ capacitor filtering technology on the mainboard to significantly reduce electromagnetic interference, ensuring stable operation even in high-dust and high-EMI (Electromagnetic Interference) environments.
🔹 Optical Protection Against Welding Sparks
Protective Cover Design: A high-temperature-resistant transparent optical shield minimizes the direct impact of welding sparks on the light curtain.
Intelligent Algorithm Optimization: Enhanced beam recognition reduces false alarms caused by welding sparks and temporary obstructions.
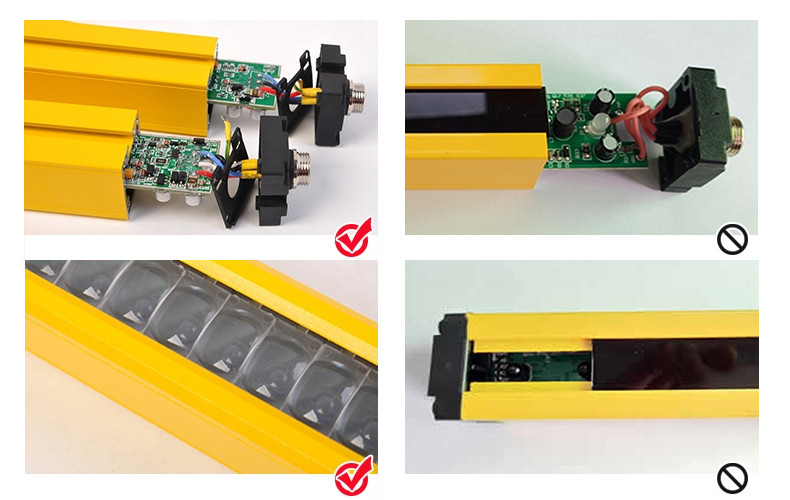
2. Structural Optimization: Innovative Installation Solutions for Improved Stability
🔹 Adaptive Installation Calibration for Anti-Vibration and Anti-Misalignment
We offer multiple installation methods to suit various working conditions. Among them, the tubular bracket installation effectively minimizes the impact of vibrations:
High-strength structural design enhances mounting stability.
Adjustable angles ensure precise beam alignment, improving positioning accuracy.
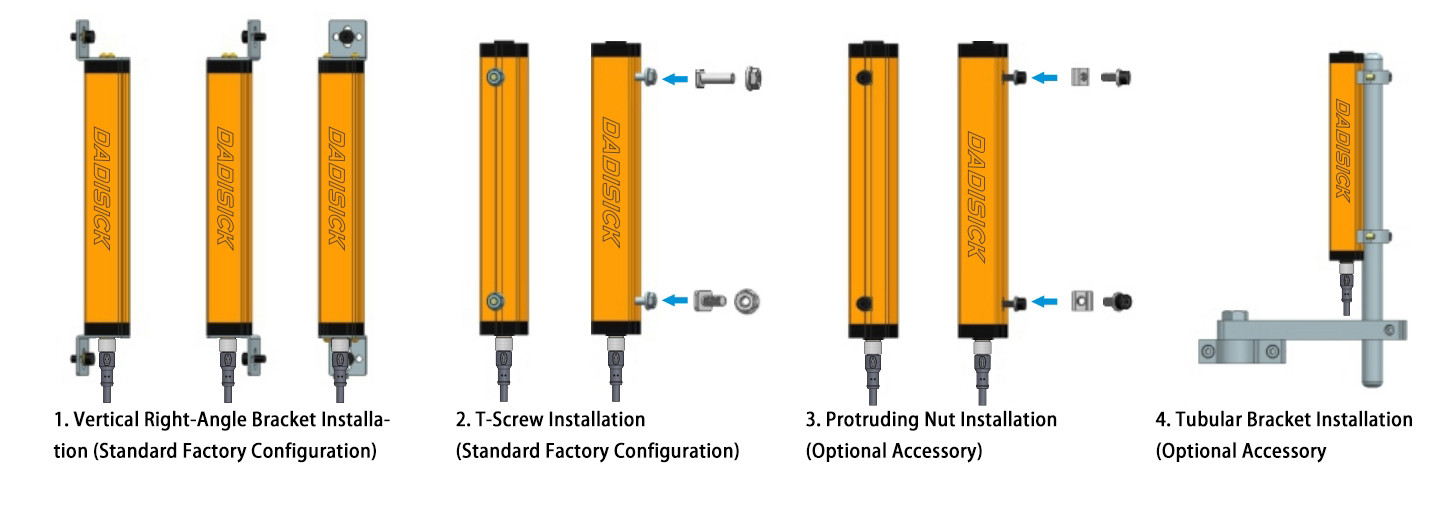
🔹 Significantly Improved Production Efficiency and Equipment Stability
"Since we adopted your company's tubular bracket installation solution, the results have been remarkable! Previously, our equipment had a false triggering rate as high as 1.0% in high-vibration environments, which caused us a lot of trouble in production.
Now, to our pleasant surprise, the false triggering rate has been reduced to 0.4%! This has directly decreased our losses caused by unplanned production stoppages by over 10%."
3. Customized Parameter Optimization: Ensuring the Best Detection Performance
🔹 Professional Calibration for Precise Adaptation to Production Needs
Our technical team fine-tunes key safety light curtain parameters based on the production cycle, robotic arm speed, and required detection precision:
Response time adjustment to accurately detect fast-moving objects.
Optimized detection range to prevent false alarms triggered by robotic arms or other normal operations.
🔹 Continuous Optimization with Long-Term Technical Support
Installation & Commissioning Phase: Engineers provide one-on-one calibration to ensure seamless integration with equipment.
Ongoing Support: Regular follow-ups and parameter adjustments aligned with production changes to maintain optimal light curtain performance.
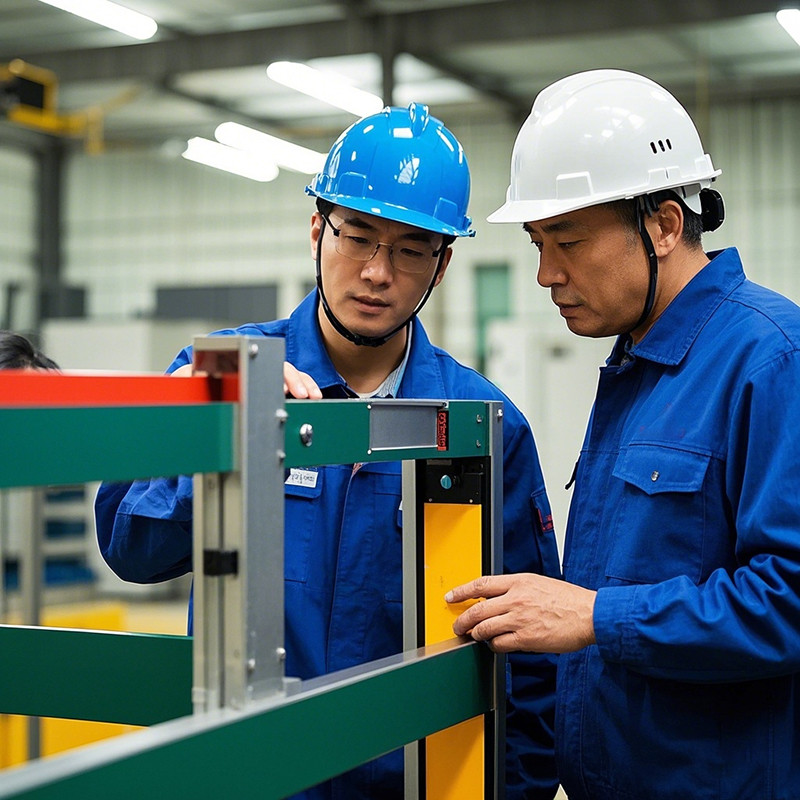
By implementing anti-interference technology, structural stabilization, and precision parameter tuning, manufacturers can eliminate false triggers in safety light curtains, ensuring smooth, efficient, and uninterrupted production.
DADISICK safety light curtains provide high-precision safety solutions tailored for automotive assembly lines, helping manufacturers reduce downtime and maximize productivity. Our safety light curtains are designed for seamless integration with traditional equipment, making them compatible with both new and existing production systems. They can be directly integrated into current setups or used to upgrade legacy systems, ensuring manufacturers can enhance workplace safety without costly equipment overhauls. With flexible installation options and customizable configurations, DADISICK light curtains offer a cost-effective way to modernize safety measures while maintaining operational efficiency.
Safety Light Curtain Replacement Solutions
DADISICK is a professional manufacturer of safety sensors with solid product manufacturing capabilities.
DADISICK is a professional manufacturer of safety sensors with solid product manufacturing capabilities.
DADISICK is a professional manufacturer of safety sensors with solid product manufacturing capabilities.
DADISICK is a professional manufacturer of safety sensors with solid product manufacturing capabilities.
View Catalog
Choosing Your Safety Solutions
You May Also Be Interested In
Disclaimer: The brands and specifications shown on this page are for product comparison and selection purposes only. Our safety light curtains are manufactured by DADISICK and are not official products of the listed brands. DADISICK offers replacements compatible with these brands' products. We do not own the rights to any of the mentioned brands. If you need to purchase official brand products, please contact the brand official representative.